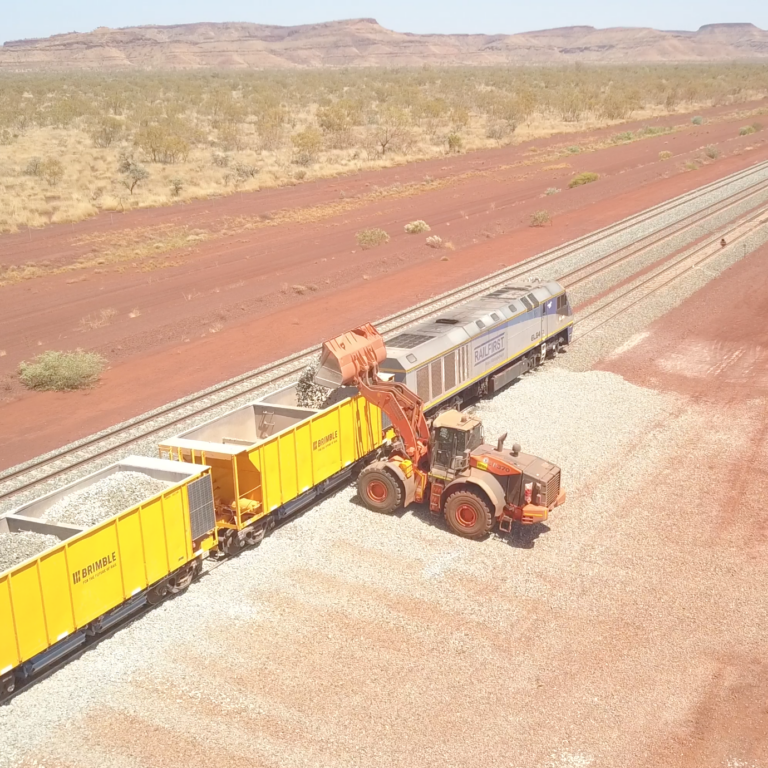
Enhancing worker safety in ballast delivery.
Brimble has recently upgraded its full ballast wagon fleet. The technology upgrades not only improve the efficient delivery of ballast material but also keep workers safer while doing so.
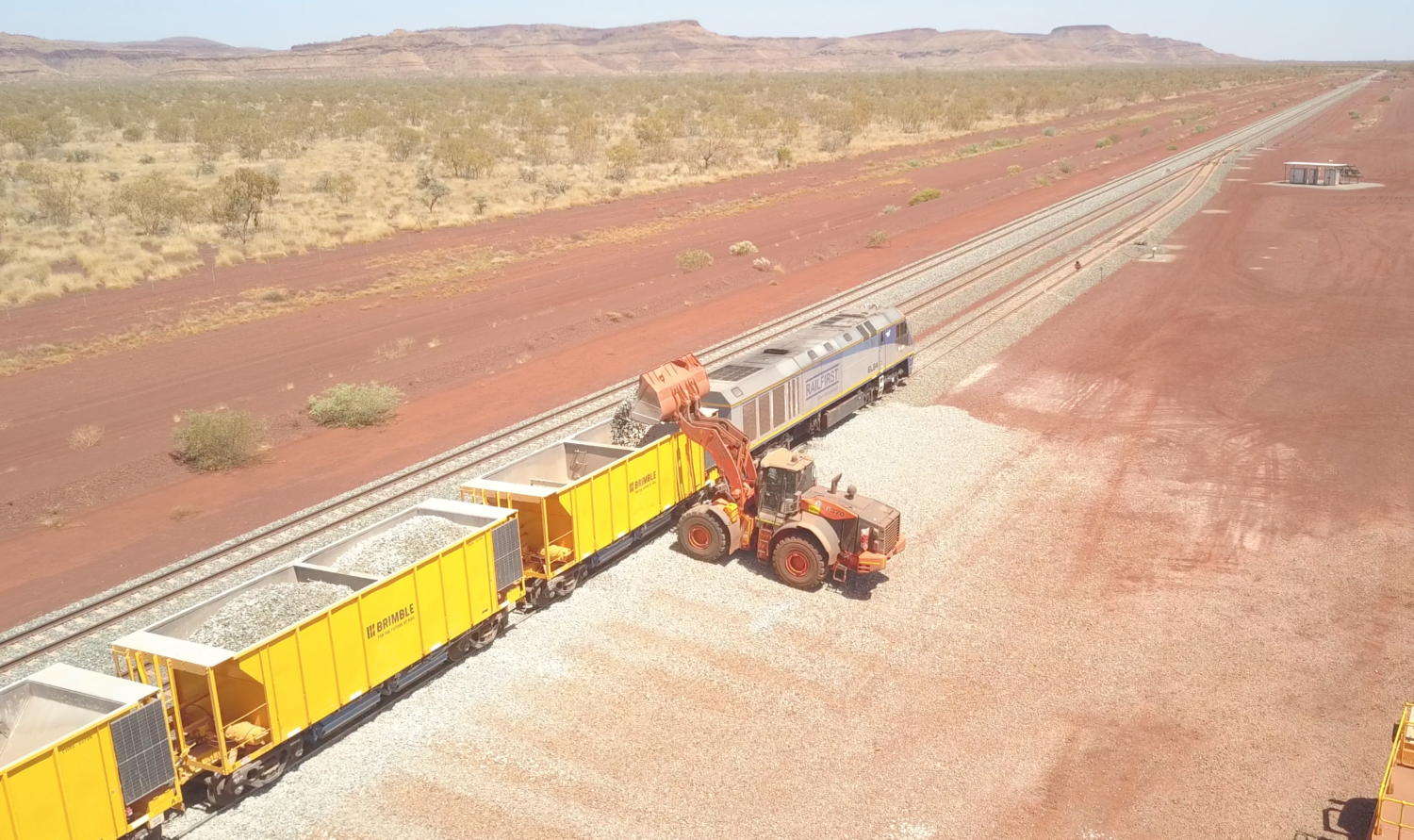
Brimble has recently upgraded its full ballast wagon fleet. The technology upgrades not only improve the efficient delivery of ballast material but also keep workers safer while doing so.
The customised wagons are controlled remotely, allowing operation in remote locations and reducing interaction time between workers and the drop zones, Steven Johnson, Brimble’s General Manager of Operations East explained.
“By limiting contact time and using technology that allows to complete work remotely, we are keeping sites safer for the team,” Johnson said.
“We are also upskilling them on technologies such as using drones for visuals in hard-to-access places.
“The HMI tech we have integrated into the machines removes all the failing switch components and gives the operator a better visual over what’s going on in the machines’ brains and more options for changes on the run.
“Digitalising these components minimises issues that can slow and even halt operations.
“If we are working in remote areas of South Australia or Western Australia for example, we no longer need to wait for technicians to attend on-site. We can rectify it remotely, often decreasing downtime in the field.”
Brimble also utilises wireless HMI operation of the hydraulic actuated hopper doors, a unique technology in Australia that allows the ballast to be dropped in more precise locations.
The ballast wagons are ‘open to work’ and ready for use on 2024-2025 projects Johnson said..
“We’re proud to be making things more intuitive and safer for our workers through this technology, and it’s creating better results for our clients across Australia.”